Back from lunch, I picked up my next assigned vehicle: a 2007 Chevrolet pickup. The VIN check revealed a 5.3L V8 engine paired with a 4L60E transmission. The customer reported a slight shudder during acceleration, particularly noticeable when merging onto the highway. Grabbing the work order, my trusty Snap-on scanner, I headed out to diagnose the issue. "This shouldn't be too complex," I thought to myself.
The next step was to plug in the Zeus diagnostic scanner. The system scan revealed trouble codes: P0171 (Fuel Trim System Too Lean (Bank 1) and P0174 Fuel Trim System Too Lean (Bank 2). In simpler terms, the engine computer is detecting that the air-fuel mixture is too lean, meaning there's not enough fuel compared to the incoming air. Lean conditions are relatively common, but they can point to a few different problems. A lean fuel mixture can result in reduced power, engine hesitation, and even increased emissions. It's important to diagnose the cause promptly to avoid further issues.
With the codes in mind, I strapped myself in and hit the road for a test drive. My initial hunch leaned towards one of two possibilities regarding the customer's original concern: a misfire or a torque converter shudder. The shudder typically manifests as a vibration felt during acceleration, while a misfire can cause hesitation or a jerky feeling.
I cruised down the frontage road next to the shop, pushing the truck up to around 45 mph when traffic allowed. Initially, I couldn't detect any problems. However, after 10-15 minutes of driving and letting the engine reach operating temperature, I felt the issue the customer described. It presented itself most noticeably between 40 and 50 mph while maintaining a steady throttle on an incline.
To rule out a torque converter issue, I monitored the live data stream on the scanner and focused on the torque converter RPM slip PID (parameter identification). This data point essentially shows how much the engine RPM and transmission output shaft RPM are differing under load. A normal reading here would indicate the torque converter is functioning correctly. Thankfully, the data confirmed that the torque converter was operating within expected parameters.
Shifting my focus to the engine, I switched the scanner to display engine related PIDs, specifically those that could indicate misfires. While I could feel a slight hesitation under load, I wasn't seeing any traditional misfire counts on the scanner. This was a bit puzzling. The engine wasn't behaving in a way that typically accompanies misfires, yet there was a definite issue under specific driving conditions.
One final clue came from the live data. The mass airflow (MAF) sensor readings seemed normal, indicating the expected amount of air entering the engine. However, the fuel trim readings, which reflect the engine's attempt to adjust the fuel mixture based on sensor inputs, were showing a lean condition. This conflicting data — normal air intake but a lean fuel mixture — would be a key piece of the puzzle moving forward.
Returning to the shop, I raised the truck for a visual inspection. While there were no transmission leaks to worry about, a familiar engine oil leak told its own story. As I was closing the hood, something caught my eye; the top of the engine was unusually clean. Removing the engine cover revealed blue intake gaskets and a spotless throttle body. This immediately triggered a hunch. These were telltale signs of recent top-end work, and it aligned with the presence of the lean condition codes and the evidence of the previous oil leak. I had the service adviser call the customer to inquire about recent engine work and the customer verified that the issue seemed to have started after the repairs were done, but the shop dismissed it as a TCC shudder and referred him to a transmission shop. That is why he ended up at our facility.
To be thorough, I followed the standard procedure: checked the air box and snorkel tube for leaks or damage and inspected the MAP sensor, which had been replaced according to the code descriptions. Finding nothing out of the ordinary, I focused on the fuel injection system.
Remembering a similar case that I'd dealt with at another shop where misconnected fuel injectors had caused similar symptoms, I thoroughly inspected the wiring for each injector. Sure enough, it turned out that injectors #5 and #7 had been crossed during the previous work. (Figure 1)
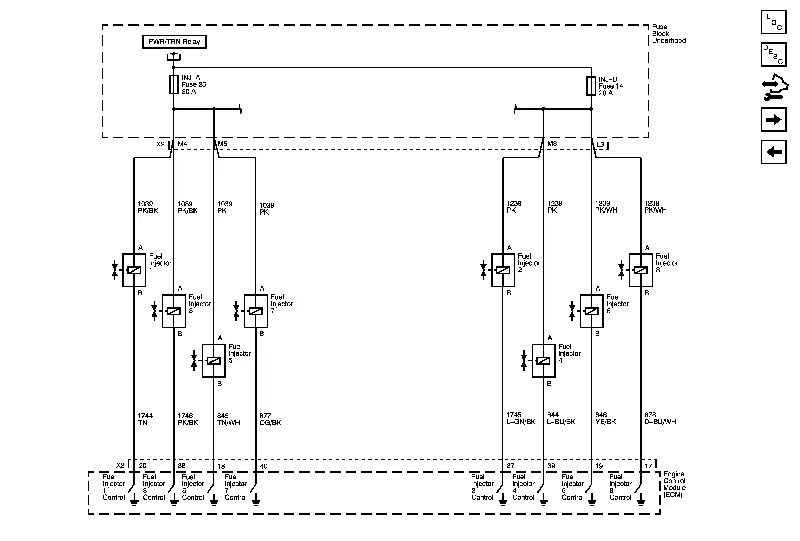
Figure 1
I corrected the connections and prepared for a road test, feeling optimistic. (Figure 2)
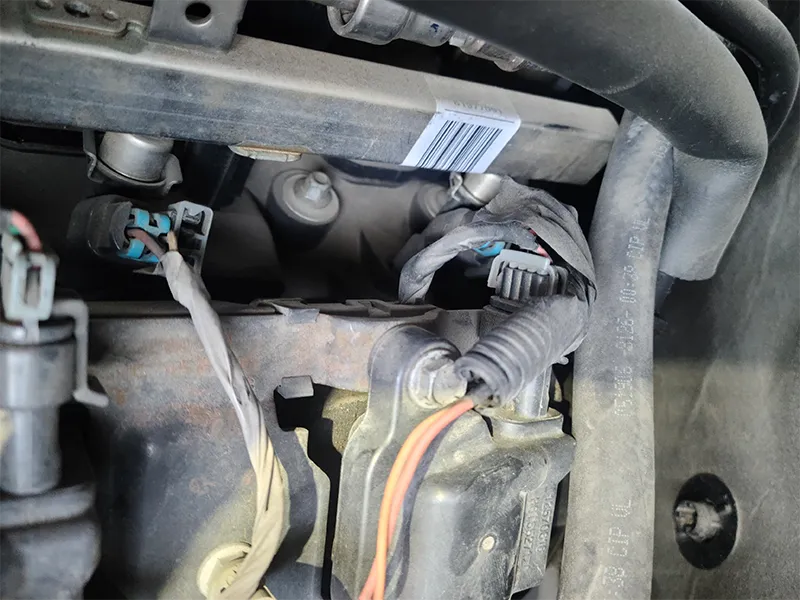
Figure 2
After clearing the codes and resetting the fuel trims, I embarked on a final 30-minute test drive. The results were immediately clear; the drivability issue was gone! While a transmission repair wasn't the answer this time, the careful diagnosis and solution earned us a satisfied customer for life.
While this is an older application, this scenario could happen on any vehicle. As a specialty repair shop, we don't have the luxury of seeing the entire repair history of a customer's vehicle. While we certainly have very loyal customers, the previous repairs made to this truck is work we don't perform. Therefore, we must look for clues and then consult the customer. Instinct, evidence, and clear interpretation of the diagnostic data saved us on this one.