Our shop recently diagnosed a 2008 Chevy Silverado 3500 tow truck from a local towing company. The customer's complaint was that the vehicle would set intermittent erratic transmission codes and intermittently go into fail-safe mode. The driver of the truck also stated that he knew this because he had his own code reader and was able to clear the codes along the way. It was equipped with a 6.6L diesel engine and an Allison transmission. My first step in diagnosing the tow truck was to perform a code scan which revealed transmission code P0761 (shift solenoid 3 valve performance stuck off).
Before I dove into following the P0761 flow chart I wanted to perform a thorough visual inspection of the truck, paying close attention to the wiring, connectors, and the condition of the harnesses. With the truck having 420,000 miles on it, it had developed some severe engine oil leaks. These oil leaks had been accumulating and soaking into the main transmission wiring harness for quite some time. (Figure 1)
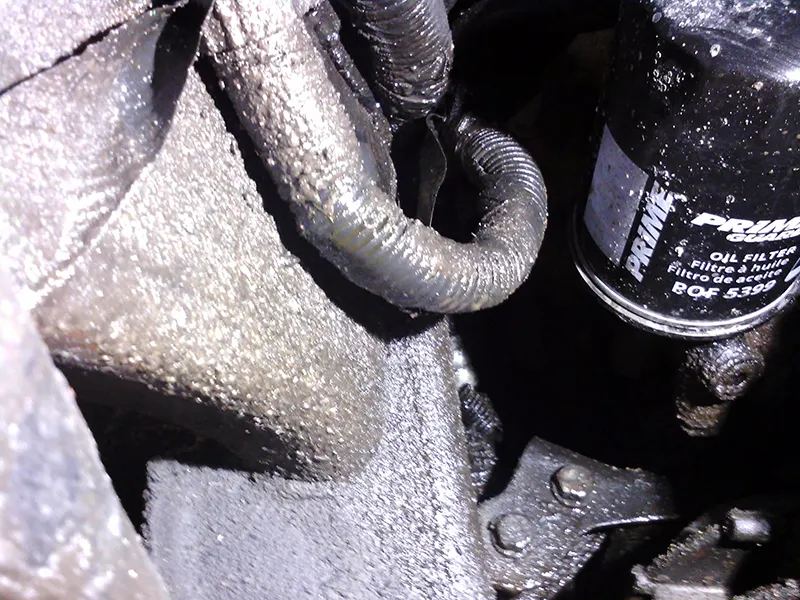
Figure 1
I say that because in comparison to new wire insulation, this wiring was so compromised it felt more like soft stretchy rubber that had been deteriorating, breaking down, and soaking in diesel engine oil for many years, probably because it had been! The customer was aware of this too, admitting that they had already received a quote for a used wiring harness for $2,300.00, which at the time was only available as a complete engine compartment harness assembly. He also had received a $3,000.00 quote for a new harness that did not include the labor to replace it. Needless to say, the tow company was not interested in paying that kind of money and declined on a complete harness swap and hoping instead we could repair it more economically.
As I followed the flow chart, I presumed the soaked harnesses were faulty, given the bad condition I had seen them in. However, the flow chart results revealed no problem found when I completed the steps which was not a surprise, given that I was dealing with intermittent codes in the first place.
Inspection of the shift solenoid connector at the transmission revealed transmission fluid leaking into the connector past the terminals; this seems common with these units. A leaking shift shaft seal was also noted, so I needed to start a parts list for the customer. At this point I added an internal transmission harness, new filters, and a shift shaft seal to my list of new parts needed. While I was replacing the internal harness and filter, it seemed like an opportune time to perform a quick resistance check of the solenoids and an inspection of the valve body, so these were added to the estimate for a little extra labor while the pan was off.
The customer gave approval to move ahead with our estimate. The valve body was sent to our VB/Sol Dept. where an inspection and vacuum test were performed, and it passed those tests. It was my hope that repairing the leaking internal harness would take care of the problem since all tests cleared other suspect components up to this point and it seemed promising since the code did not return after a 20-mile test drive. The tow truck was released back to the customer.
Six days later the tow truck came back with another transmission code. On a positive note, the P0761 code did not reset; this time the code P2727 (pressure control solenoid 1 open) was set. Knowing that the internal harness was replaced last visit and everything inside the unit was inspected at that time also, I was back to contemplating a wiring or control module problem.
The entire circuit was testing normally at 5.04?, hence the intermittent nature of the codes. I still did not feel confident in the integrity of the external wiring, knowing that the harness was in such rough shape and the customer had previously indicated he was not interested in purchasing a complete wiring harness. While the harness remained suspect, I was not interested in opening the harness to try and find the problem area since the whole harness was so oil soaked; it was a safe assumption that there was more than one problem area with this harness, anyway. So where to go from here? In my mind we would either send the customer down the road blaming the harness, or we try to find some way to fix the vehicle without too much additional cost. Since our business is to help people, we decided to try to come up with a plan to fix the current issue while making the customer fully aware that there can be other issues that arise in the future, and this was more of a ?patch? than a fix. In the interest of keeping the repair quick and simple, I quoted them the cost of running two new wires for the PCS 1 from the TCM to the transmission. Those were most germane to the symptoms.
The customer gave the go-ahead on the patch wiring repair. The customer had also done some intense web-searching about the issue and found information that there had been some TCM issues with this model year vehicle, so he requested that a new TCM be installed, also. The TCM was replaced, programmed, and two new pressure control solenoid wires from the TCM to the transmission were run. The truck was then released to the customer after another successful test drive with no transmission codes.
After three days and over 500 miles driven the truck arrived back to the shop and had set a code. The code it set this time was P0716 (input/turbine shaft speed sensor A circuit range/performance). So much for intermittent codes being set by the TCM! Since the pressure control solenoid code had apparently been repaired by the new wiring, I could only assume the wiring was the issue causing the speed sensor code, or possibly an intermittent issue with the speed sensor itself. After some checking I did find that the ISS wires were shorted together between the TCM and the transmission.
The customer gave the authorization for the repair once again, so I replaced the input speed sensor wiring making sure that the speed sensor wiring was a twisted pair. The easiest way I know to do this is to clamp the ends of two wires in a vice and the other ends of the two wires in a drill. Then slowly turning on the drill until the recommended 9 to 12 twists per 12 inches of wiring is achieved. (Figure 2)
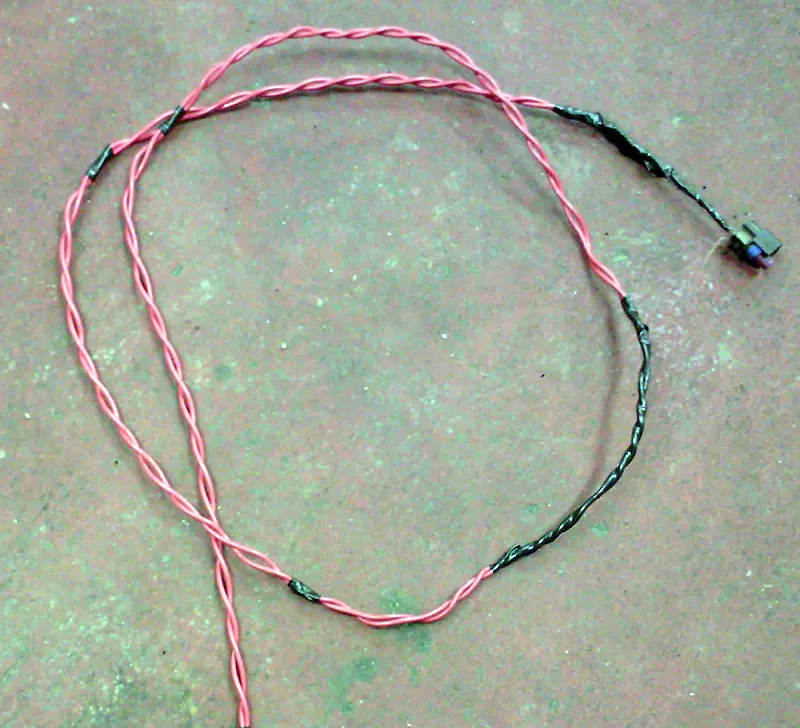
Figure 2
After another successful test drive the truck was returned to the customer.
The customer has been driving the tow truck now for almost a month without any further issues or transmission codes. It may have taken a little more time to get all of the intermittent codes repaired as they occurred, but it was definitely much cheaper than a new, or even a used, harness replacement.
This was by far not the best situation as far as a fluid diagnostic process, mostly driven by the customer's need to get the truck back on the road ASAP and not wanting to invest in the expense of an external replacement harness, but all in all we did get the customer back on the road and repaired within the budget, at least for now. Sometimes it is inevitable that the customer's budget will preclude a precision repair, and it can be a tough decision to perform a less-expense patch repair or refuse he job altogether. In this case, we hope that this customer remembers us when it's time for another service.