For this month's article, I am going to lay this out like a "case study" but the procedure used to find the root cause of this issue can be used on almost any application. I am going to use the scope module that is part of the Snap-On Zeus scan tool; is this the best scope out there? No, but ease of use and the addition of the "guided component tests" makes it an easier process for technicians that are not used to using a scope.
We had a traveling customer that was visiting family in town and their 2005 Jeep Grand Cherokee started intermittently going into failsafe mode about a hundred miles outside of town. While listening to the radio they heard a commercial for a transmission shop that claimed they fix your transmission and just not sell you a new one. This is where the story begins.
The shop checked the Jeep out and told the customer, "...the transmission has a solenoid code. This solenoid is part of a "solenoid pack" that needs to be replaced and the cost is a lot less than a new transmission." The customer gave authorization for the repairs to be completed. The vehicle is then returned to the customer, and the next day a code sets and the transmission goes into limp mode again, so the customer returned to the original shop.
At this point the customer loses faith in the repair shop. The adviser said, "We already replaced the solenoid pack, so it must need a computer. The bad solenoid must have damaged the computer."
The customer declined the repair and did a web search for transmission shops. Focusing on the best-rated shops in the area, the customer found one of our shop locations. When the customer arrived and told us the whole story, we told her that we would accurately diagnose her concern and guarantee the repairs.
The Jeep would intermittently set a P0750 code when hot, so we started the diagnosis. We started with a battery and charging system test, checked fluids, visual inspection, etc. We hooked a DVOM up to the L-R solenoid at the case connector and it ohm checked fine. We weren't expecting to find an issue there, but we had to start from scratch. We cleared the code and went out for a road-test. After driving for quite a while, the P0750 code set again as a "pending code" and after the first time the code set the transmission went into failsafe mode. (Figure 1)

Figure 1
We went back to the shop to dig a little deeper into this issue. This is where the process can be used on any application where a computer-controlled load (solenoid, in this case) is in play, whether it be a duty-cycle or just an on/off type solenoid. I am not saying this is the only way to do it; it is just the way that I have found to be easier/quicker to find an intermittent issue like this.
I back-probed into the L-R solenoid circuit at the PCM and connected that to channel 1. I then connected a current clamp further up the circuit and assigned it to channel 2. This would allow me to look at both the voltage at the control side of the circuit as well as the amperage simultaneously. (Figure 2)
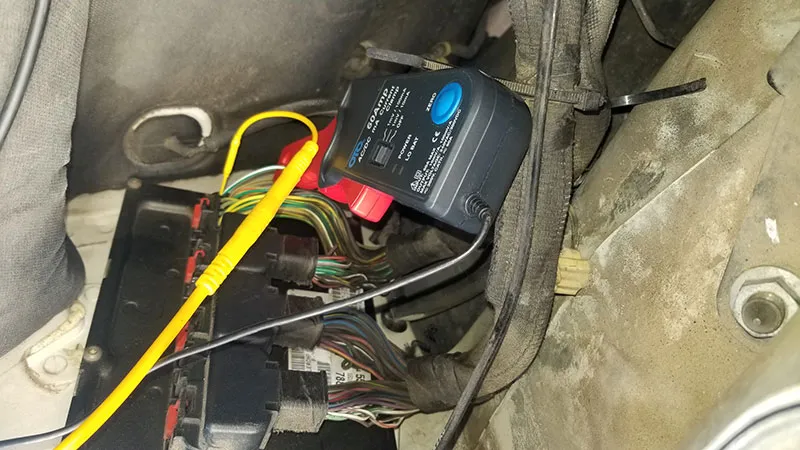
Figure 2
When everything is working correctly it is going to look like this on the scope: (Figure 3)
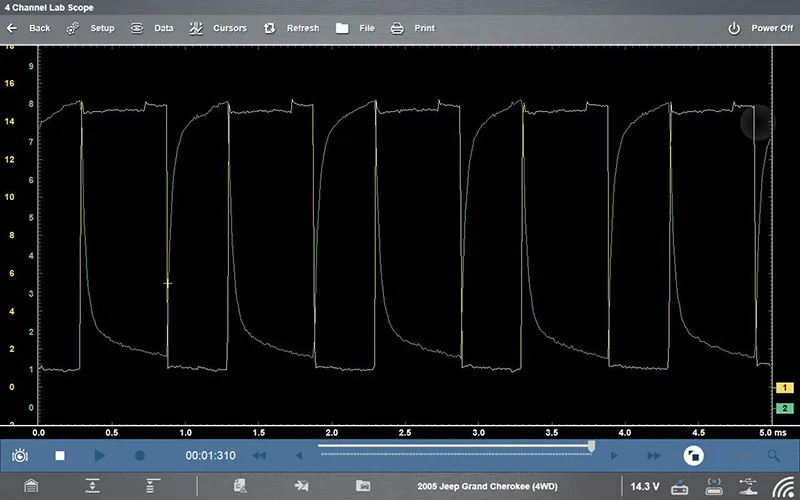
Figure 3
With everything connected and the wires routed safely in order to avoid rubbing or pinching anywhere, we were off for another road-test. Just like the first time, it took some time for the code to go active again. I did have someone assist for the second road-test as the stop button on the scope needs to be activated close to the event so you can save the recorded data during the time problem happened, so we saved a couple recordings and headed back to the shop to review them. I was confident I was able to capture the data that showed the problem.
The following images show the first and second time that the problem occurred, and without zooming in, you can see the entire event. However, in this circumstance the fault happened three times before it set the code. (Figure 4 & 5)
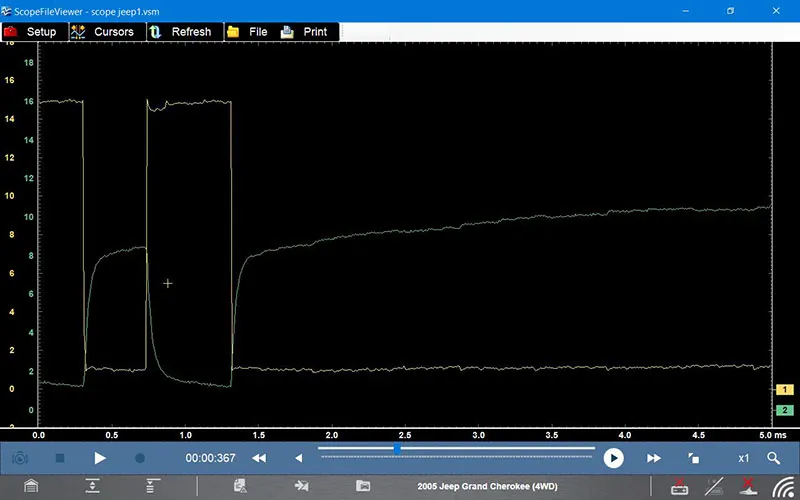
Figure 4
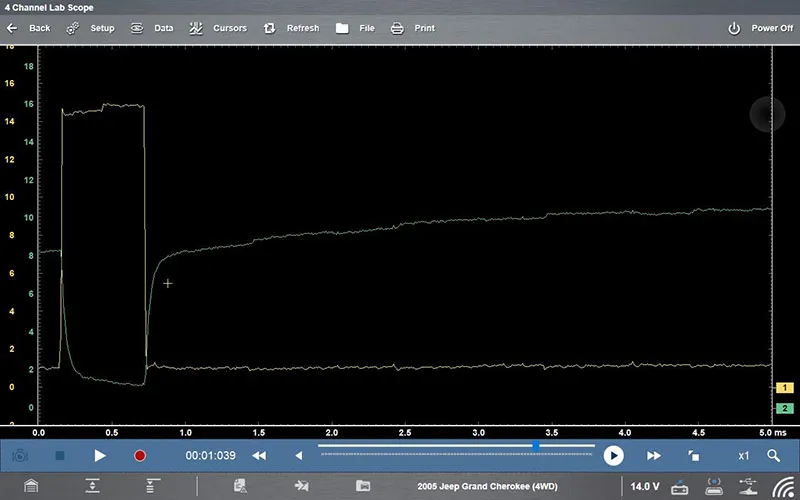
Figure 5
I am not an internal computer component expert, so I am probably not the guy to say exactly what happened inside the PCM to cause this, and I am not going to fix a controller, I am just going to replace it. I will hypothesize that it looks like the driver inside the PCM stuck on somehow and pulled the circuit to ground; this "event" lasted 8ms. Here is the zoomed-out view, and the issue starts at approximately 22m: (Figure 6)
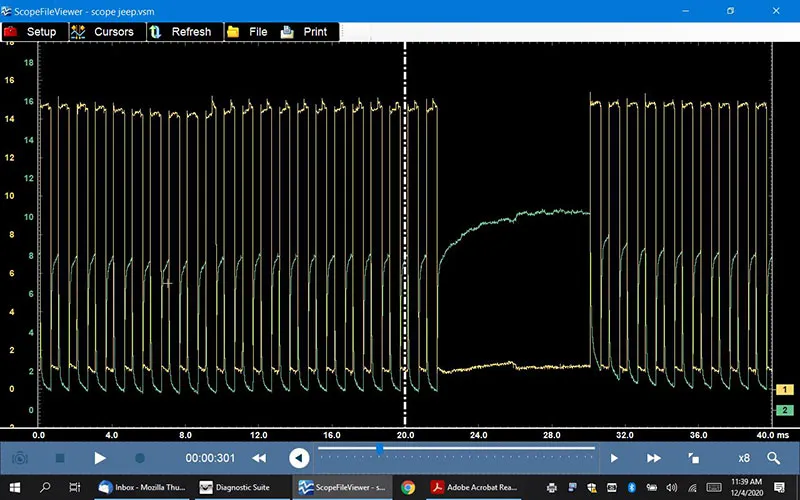
Figure 6
This image shows what the scope looks like when the code goes active. This is zoomed out quite a bit to see the whole event. (Figure 7)
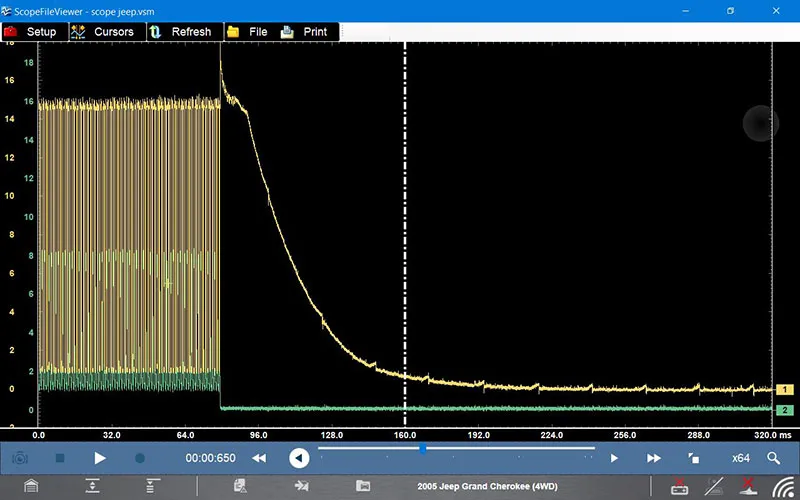
Figure 7
8ms and three separate events is what it took to set this code. There is no way that a DVOM would capture this issue; I'm sure you could guess or throw some diagnostic darts, and eventually you are going to hit your target. Heck, the first shop's second guess would have been correct!
This method is not the only way you can find a bad circuit, bad ground, bad load device, or bad ECU. If you are just starting out using a scope, you don't necessarily need experience to spot a problem. It certainly helps, but most of the time you will have a good scope pattern to look at and compare to. In this case, the unit is setting an L-R solenoid code, so all you would have to do to find what "normal" looks like by moving your connections to another solenoid that is NOT setting a code, and now you have a perfect example of a good scope pattern to use as a comparison against your suspect solenoid circuit.
In close, most shops have equipment with features that some techs might not use due to perceived complexity. These features can be huge time-savers that equate to more profit and better "first-time-fixed" service for your customers. Review what you have and learn how to use these tools.