By now, everyone in the automotive industry should be aware of the infamous Nissan radiator issues that cause antifreeze to contaminate the transmission oil (and vice versa). If you're not, you should research the topic as the implications are many. This issue isn't as easy to detect as it was several years ago. Today's transmission fluid doesn't always tend to froth up into the "pink milkshake" that was always a telltale sign of contamination. Small amounts of glycol can wreak havoc on the transmission, and many times a test kit is required to detect it. I know this is nothing new, but perhaps a refresher with a few new things that you may have not previously considered. The vehicles I will be referencing will be a 2005 Nissan Pathfinder 4?4 and a 2007 Nissan Pathfinder that had related issues all within the last six months.
The 2005 Nissan Pathfinder case started as a carry-out transmission installed by a wholesale customer. This vehicle came back to the shop with a torque converter shudder after being driven less than 2K miles. We started with a standard preliminary evaluation and the visual inspection revealed that there was transmission fluid in the coolant as evidenced by the "purple milkshake" in the reservoir. We also found some transmission fluid in the radiator that had been previously replaced along with the transmission. This was alarming, but to prove it a sample of the transmission fluid was captured for testing.
The fluid test exhibited trace contamination of ethylene glycol in the transmission fluid. After repairing the transmission damage, pulling the radiator to have it pressure tested was in order. The radiator tested out ok, so this case was even more perplexing. Our first thought was that the original installer didn't flush the lines or auxiliary cooler when the transmission was replaced. At this point we felt that flushing the cooler lines and auxiliary cooler should take care of the remainder of the vehicle issues. This also required flushing of the engine cooling system to clean out the transmission fluid.
After completing the road test and with everything working properly, we took a sample of fluid to run a test for ethylene glycol only to again find trace amounts of glycol in the fluid! How could this be? After some head scratching we determined that the auxiliary cooler had small amounts of anti-freeze trapped in it that flushing apparently didn't force out of it. Now that we were aware of this issue, the next step was to replace the auxiliary cooler and road-test again. This completed the repair. It is hard to understand why the auxiliary cooler wouldn't clear with the flush machine that we use, but because of this discovery, it is now standard procedure for us to replace the radiator and the auxiliary cooler on these vehicles when replacing the transmission.
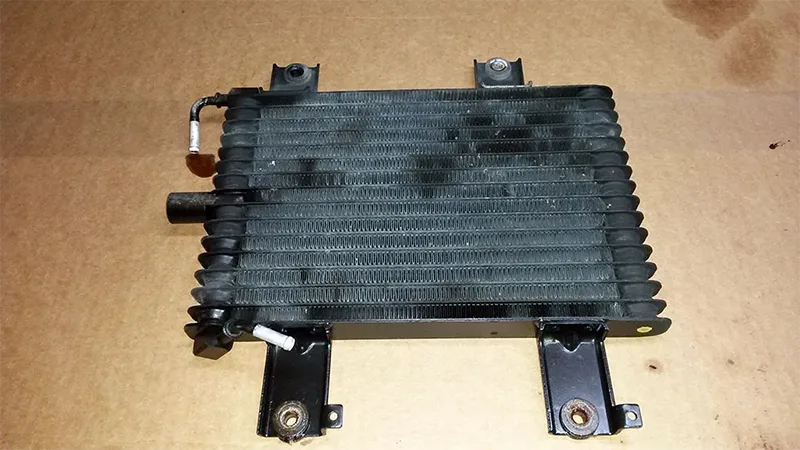
Figure 1
The next case was a 2007 Nissan Pathfinder. This one arrived with coolant in the transmission, and transmission fluid in the coolant. After going through the same steps of transmission replacement as the previous case, replacing the radiator and auxiliary cooler, then flushing cooler lines and engine cooling system, you would think that all the bases would be covered, right? Nope. It would seem that the rubber components in the cooling system do not play well with transmission fluid! As if.
There were additional clues that this one seemed to have been contaminated for a longer period of time, as evidenced by very soft radiator hoses. After the radiator hoses were replaced, we figured that we'd found the last of the glycol issues. Alas, the problems continued. The darn engine was running hot. We had a new radiator and the fan was working, so the next step was to take a look at the thermostat.
Well, well, well. The rubber swelled to a point partially restricting the flow of coolant to the engine.
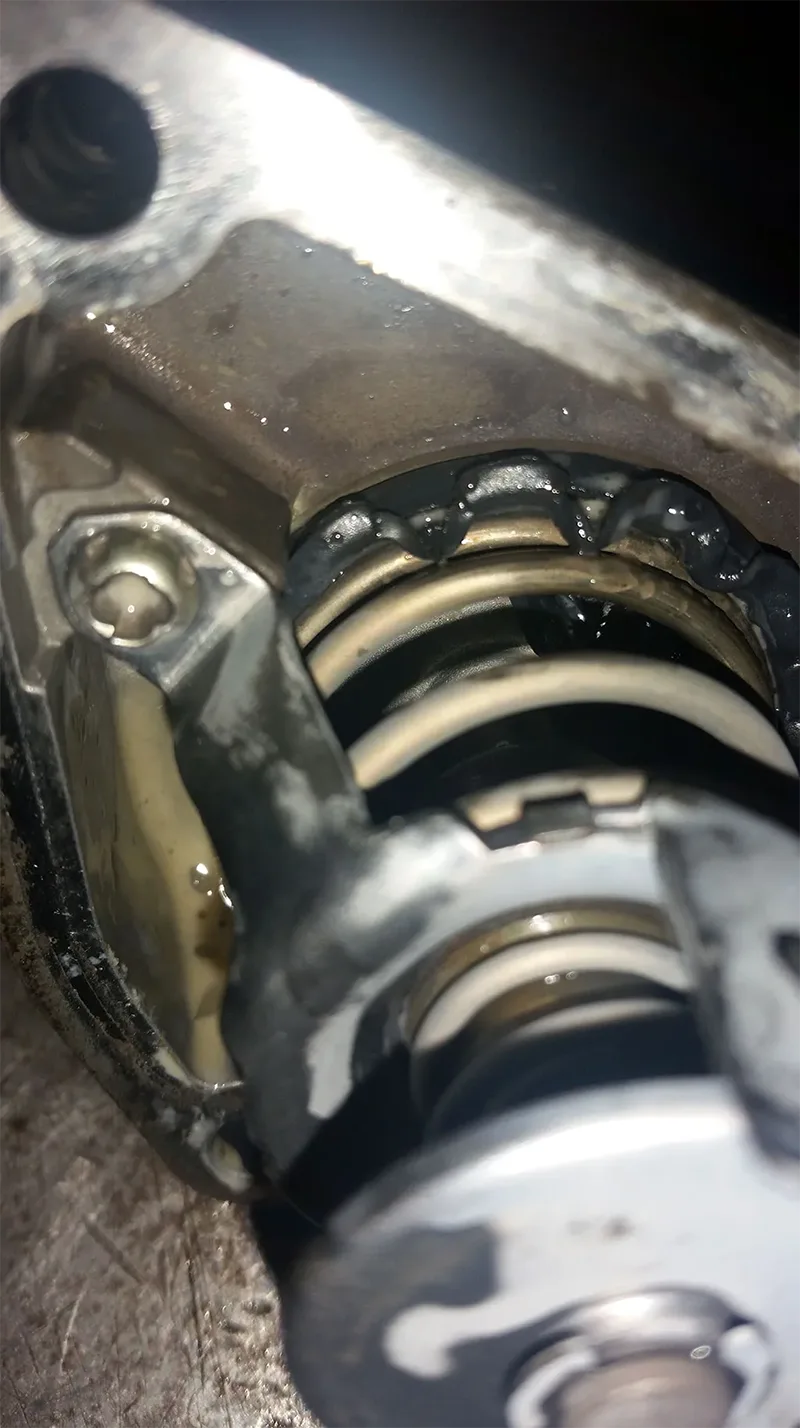
Now this begs the basic question: where does it end? Clearly every gasket and seal in the cooling system is now suspect to failure. How do you convey this to a customer so that they can understand? Facing increased repair time, labor, and parts becomes a hard sell. It's always in the best interest of the customer to sell them what they need in order to prevent a future failure. Sometimes they can't see beyond what is broken "right now", so it's our job to thoroughly explain these issues to them until they're confident in paying you what it takes to accomplish this.
These cases illuminate a need to think about the full scope of damage that could be incurred by a related system failure when they interact with each other. While not necessarily common, it's the extra thought and perseverance that keeps customers coming back to your shop. "Fix it right the first time" is something to live by. Learning what to watch for is half the battle, as shown here.